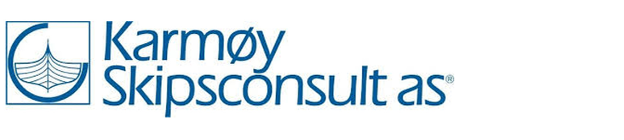
Automation of Product Information Management Brought Clarity and Efficiency to Ekeri’s Operations
Challenges
- Manual work in design and production slowed down the information flow and increased the possibility of errors.
- Incompatibility of component lists and articles: BOMs created in CAD software were not directly linked to the ERP system, making data management difficult.
- Lack of unique component identifiers: Many components were only defined by drawings and raw materials instead of having their own article numbers.
- Inaccurate material quantities: BOMs were often based on averages. The same BOM was used for different product sizes, leading to inventory-level errors and material requirement miscalculations.
Solutions
- Integration of Sovelia Core and Sovelia Configurator with CAD and ERP systems.
- Efficient management of articles and component lists with Sovelia Core.
- Use of Sovelia Configurator for customer-specific product creation and publishing.
- Utilisation of Sovelia for managing technical documentation and certifications.
Benefits
- Reduced manual work
- Lower risk of errors in both design and production
- Faster information flow between sales, design, and production
- Improved design accuracy
- Real-time and up-to-date information across different systems
- Efficient management and production of customised solutions
- Enhanced competitive advantage and better customer service
- Complete traceability of all product and manufacturing data, facilitating quality control and error tracking
- A centralised PLM system prevents the use of outdated information through version control