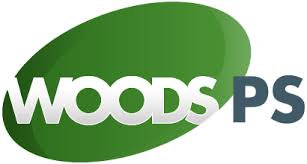
Pindstrup’s Pan-European Design Team Embarks on a Digital Transformation Journey
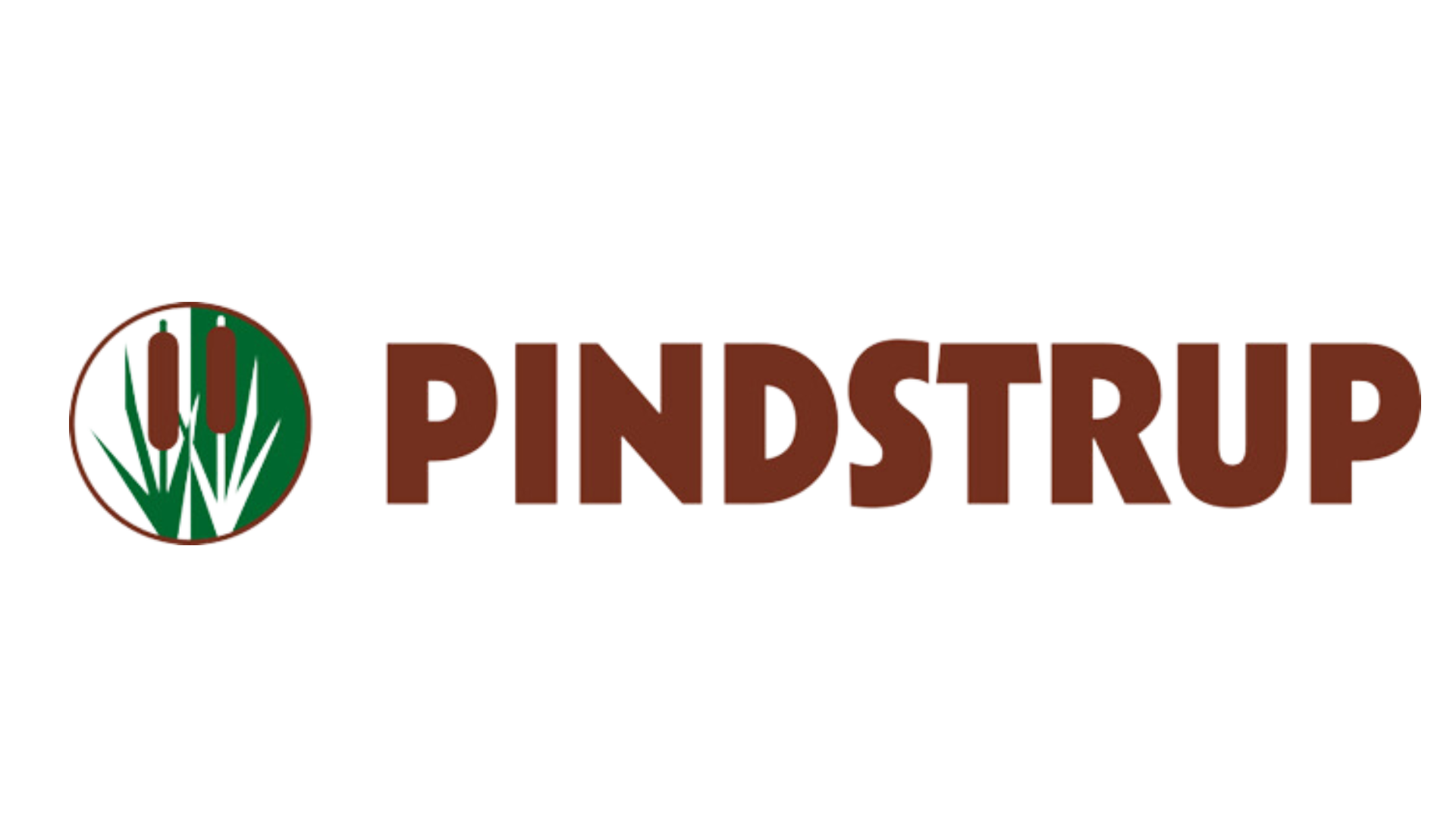
Collaborating Across Multiple Locations, the Team Uses Vault to Speed Up Factory Modernisation
Founded in 1905, Pindstrup is a global leader in producing high-quality growing media for professional growers. Committed to sustainability and innovation, Pindstrup designs and builds its own processing lines with a diverse engineering team across Europe and the UK. Seamless collaboration is essential for the company, made possible through a beneficial partnership with Symetri, which is working closely with the Pindstrup team to provide invaluable support and guidance throughout the entire modernisation process.
“We design and build our own processing lines and associated equipment at Pindstrup, with a diverse design and engineering team across numerous locations both in the mainland Europe and the UK. A critical need in this regard is being able to collaborate no matter where the project members happen to be located. Today, Vault makes all that possible, but arriving at this perfect state has been something of a journey. Symetri has been alongside us all the way, providing expert guidance through each phase of our modernisation and, in so doing, being an invaluable support for the expansion of engineering team at Pindstrup. We trust their advice, we value their input, and we truly appreciate their dedicated, personal approach.”
David Walker, Head of Technical Department at Pindstrup
Meet Pindstrup
Founded in 1905, Pindstrup Mosebrug A/S (Pindstrup) is one of the world's leading producers of high-quality growing media for professional growers, serving customers in more than 100 countries. With its head office in Denmark, the Pindstrup Group has production sites in Spain, Latvia, Estonia, Brazil and Northern Ireland, the latter serving the UK market through a subsidiary company, Bulrush Horticulture Ltd. The Pindstrup Group has more than 800 employees, all dedicated to helping growers across the world. In its early decades the company was involved in various activities, one of which was the cutting of peat blocks for heating. Peat was also sold as livestock litter. In the 1960s, the use of peat for heating began to decrease, and the company looked for alternative outlets for its products. This led to entering the horticulture business as a supplier of growing media, which at the outset were mainly peat-based. Today, almost 30% of Pindstrup’s raw materials are alternatives to
peat – a number that will continue to increase as the use of peat is reduced.
The most important peat alternative for Pindstrup is wood fibre. Initially developed by the Bulrush subsidiary in the 1990s, Pindstrup today produces wood fibre at a large plant in Latvia and is actively working on three new wood fibre plants.
The move towards wood fibre and other renewable raw materials is a key element in
Pindstrup’s strategy and its wish to help grow a responsible world. The processing of several raw materials adds complexity to the plants and requires efficient workflows, which is why the technical department and their work are key to the successful delivery of high-quality, consistent products to customers all over the globe.
The design/engineering need for collaboration
Given that Pindstrup’s principal activity is the production of growing media, it may appear that design software has no great part to play. It is, however, essential in making sure that the company’s factories/processing plants operate at optimum efficiency.
This involves leveraging the very latest CNC machinery, and delivering the safest and most sustainably designed solutions that enable Pindstup’s products to keep pace with a huge horticultural market; both on the professional side (large-scale growers) and within the retail market (for home use). The factory floor is where everything that happens in the design team comes to life.
David Walker is Head of the Technical Department at Pindstrup. He has been with the company since 1993. David heads a team of three engineers, two designers and a number of subcontracted designers. Their overall remit is to create the machines used in the factories, to modify them as developments evolve, and to make sure that the company stays in the forefront of modern methods of horticultural product processing.
Collaboration should be a solution, not a challenge
We design all our own machinery, from the cutters, to the conveyors, to the computer-controlled dosing systems, to the balers and packing machines. The team is based in different locations, different countries, and often working from home. Collaboration on drawings and models is mission-critical. It always has been. But there was a time not that long ago when making collaboration possible was a challenge in its own right,” says David.
In 2007, Pindstrup started working with Symetri; at a time when collaboration in design relied solely on sending design updates between team members via email. Real-time collaboration was evolving as a concept, but not entirely realisable.
“When we first started using Symetri, it was for software purchasing and licensing. We quickly discovered that they offered so much more than that. Meeting various tech experts from the team, we felt we could gain considerable value from their expertise and their knowledge of developments in technology, particularly in the field of manufacturing”, says David.
Working as one integrated unit - The Collaboration Challange
At that time, David and his team were using Autodesk products for design requirements.
“We needed more flexibility than our existing approach gave us,” says David. “Symetri recommended Autodesk Vault as the optimum way of streamlining our workflows. Initially, Vault was implemented at the Bulrush site. After seeing what it could do for us and having trialled it on one or two test projects, we rolled Vault out across all our European sites. It also enables us to share views with our contracted designers.
Their intra-company communication on the design was facilitated by three satellite servers at three sites, with the master server based in an independent off-site location. Centralisation of design data across all sites was key, enabling both designers and stakeholders to collaborate on key projects and deliverables with ease of use, consuming and editing the data.
So, we moved from a time-consuming approach to sharing -- the old email way -- to a fully joined-up circle where the team can work as one integrated unit as and when the project requires it".
With the advent of remote working and to facilitate the wider team, both Pindstrup and Symetri decided to move Autodesk Vault from an on-premise solution to a cloud solution. This enabled stakeholders, designers, facilities, maintenance and other departments to connect, consume and edit the data from anywhere on any device.
Training and knowledge
Regarding the value that Symetri brings to the relationship, beyond software provision, David says that training from Symetri experts has been invaluable:
“Symetri has helped grow the skills and expertise of the team.
We use the training they offer when new software comes on board. It’s great to spend one-on-one time with Symetri experts to get to know how to optimise certain applications and to use the software in a way that directly addresses our needs, rather than it being a generic approach. We’ve used them in the adoption of Vault Pro, AutoCAD Mechanical, and Inventor, to name a few. I have a lot of respect for the deep level of knowledge they have at Symetri and that they pass on to us as and when needed”.
Where to now?
David’s next step will be to deploy Sovelia Vault, Symetri proprietary software that automates design routines, interfaces with Inventor, and extends Autodesk Vault’s functionalities. Sovelia Vault provides high-level property management and process automation tools that eliminate manual and labor-intensive work. It enables engineers to register design data, convert the data into general file formats (like .PDF) and share and release these files. Autodesk Vault can also be integrated with other systems like ERP and PLM through ready-made Sovelia Vault integration functionality.
These considerations are part of Pindstrup’s continuous drive to increase its adoption of digital tools and develop an ever more sustainable approach to the materials, designs, and fabrication of its factory equipment.
“Symetri is like a part of our team. They’ve guided us for almost two decades, which means they have an intimate understanding of our technical requirements, often before we do it ourselves. Their service is always fast and responsive. Their recommendations are always accurate reflections of where we need to go next and proactive. They’re part of the family”, says David.