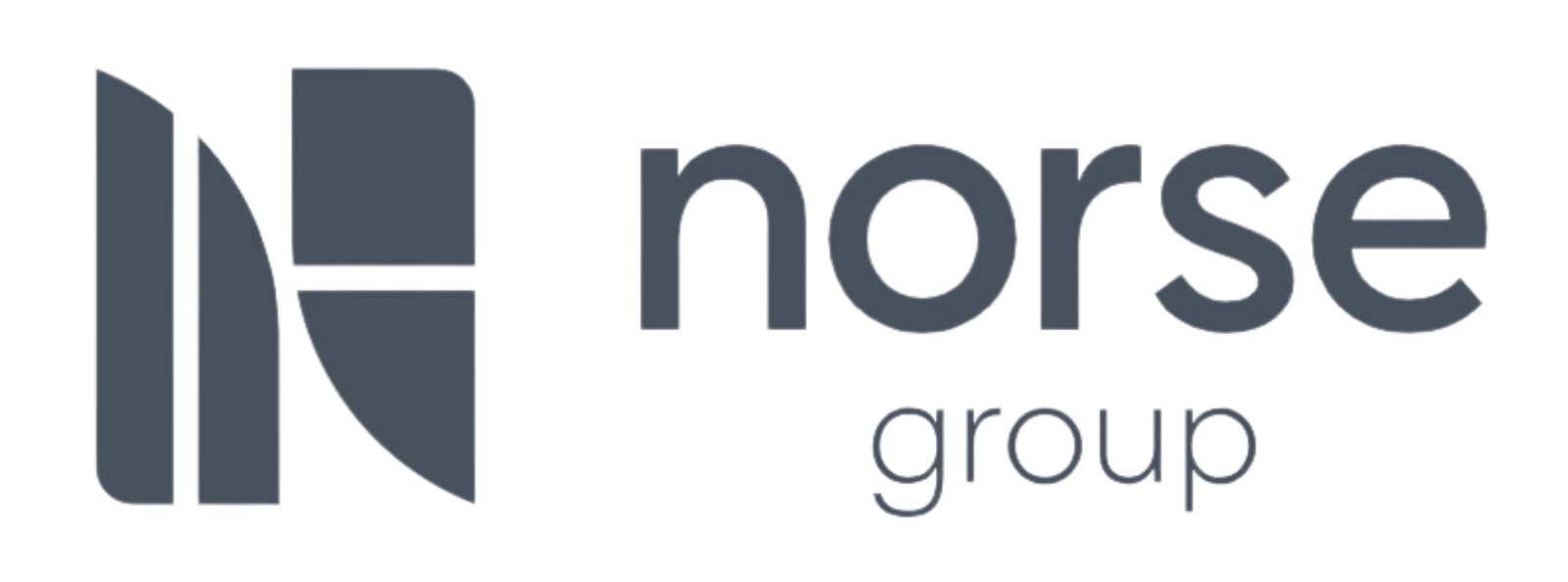
“All things technical”—Symetri’s role as trusted advisor in Stanta's digital evolution
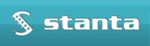
Stanta UK is a leading provider of light gauge steel stud systems and SFS infill services to the UK construction market. As the company grew and began to work on high-rise developments and government-funded projects, it became increasingly necessary to adopt more modern construction methods. Stanta turned to Symetri for guidance on how to approach these emerging requirements, and the partnership has been a success ever since. Symetri has provided Stanta with technical support, training, and strategic input to help the company move from 2D to 3D design and ultimately achieve BIM certification.
From 2D to 3D, and onwards to BIM certification
“From technical support whenever we’ve needed it, to training on specific aspects of Stanta workflows, and sorting out complex licensing issues, Symetri has always been a partner we can depend on.
There’s also a broader context to our relationship; the strategic input they give us, always with a mind to the future growth and success of Stanta’s business. The Symetri team know our business inside-out, and their invaluable guidance is now taking us to the next phase
of our digital transformation journey—empowering us for BIM certification”.
Seán O’Connor, Design Manager at Stanta UK
Meet Stanta UK
When Stanta was founded in Ireland In 2000, it was a pioneer in the use of light gauge steel stud systems. It has remained so ever since; a leading provider of SFS infill services to the UK market.
As Stanta grew, and increasingly worked on projects across the UK—from Glasgow to Jersey—it changed its name to Stanta UK, now headquartered near Stansted in Essex.
In addition to SFS substrate walls, Stanta provides window and door installations and a mixed range of cladding system installations including Insulated renders and rainscreen systems.
Stanta offers a unique ‘all in one’ design, supply and installation service for the SFS sub-contract package; for contractors, facades contractors and architectural design teams across the construction industry.
The challenge: Be modern, be exceptional, and prove it
Stanta’s activities can be defined as modern methods of construction (MMC). The company supports its clients through every stage of a project, from initial tendering, detailed pricing, operational site management and co-ordination, installation, and ongoing consultancy, through to a ‘hands-on’ approach to design. Stanta’s in-house design teams offer BIM-ready Revit framing.
It is common practice in Stanta’s part of the construction industry for contractors to outsource their design function. Stanta differs from this norm; an approach that makes it stand out to architects and contractors since they can rely on continuity across their projects. Stanta assigns a dedicated team to each project, from its inception to ongoing co-ordination of the flow of design information.
When Stanta is involved in a project, all engineering and framing drawings are prepared and issued to design programmes agreed during early consultation. Stanta believes that its approach provides greater control and assurance to clients of the commitment to the critical design lead-in and confident site installation.
“In almost all aspects of the design process, Stanta is self-sufficient and self-contained, but there is a caveat to that approach”, says Seán O’Connor, Design Manager at Stanta UK.
“Our designers all have high competency software skills when they join us, gained at degree level. The missing link is having in-depth knowledge of technology developments in the broader marketplace; what we can do to keep moving forward and being able to validate our claim of being an innovative, forward-thinking company.
Modern methods of construction dictate that you stay modern, and that’s where Symetri plays an important role in extending our capabilities and recommending both the incremental and the game-changing steps we need to take to do this”.
Technology > Training > Transformation
2D to 3D—the journey begins
Sean joined Stanta in 2017. The company’s relationship with Symetri began in 2011. “Basically, I inherited Symetri, but I quickly found out why the company was considered by Stanta as very much our trusted advisor in all things technical, given their broad knowledge of the AEC sector, evidenced by many of the team having direct experience of working within it”, says Sean.
The relationship between the two companies began when Stanta asked Symetri one question: How can we be better?
Technology
Among Symetri’s initial recommendations was that Stanta adopt the Autodesk Product Design and Manufacturing Collection (PDMC) which provides an integrated set of 2D/3D CAD, CAE, and CAP applications thereby affording a broad range of design capabilities to Stanta. Not least, from Stanta’s perspective, was the inclusion in the PDMC of AutoCAD and Showcase; the latter being 3D visualisation and presentation software that Stanta began using for CGI images. Meanwhile, digital evolution was continuing apace, and by 2014/2015 transformation in the sector accelerated. Building Information Modelling (BIM) was on the near horizon.
It was becoming increasingly beneficial, and possible, to collaborate more closely with clients and other contactors. It was also becoming possible to communicate design intentions to a way in which clients could far more easily understand the intended outcome of a design. Stanta was becoming increasingly involved with high-rise developments and particularly with government-funded projects which, by 2016 required the application of BIM practices in planning, managing, and collaborating on projects.
Stanta asked Symetri to advise on how to approach these emerging requirements, Symetri suggested the time was right to switch to Revit and recommended the Autodesk AEC Collection both for the breadth of solutions it offered, and the connection it would give Stanta to the way in which architects were working and in which clients wished to view projects.
“We were reluctant about the AEC Collection at first, since it contained so many programmes we felt we’d never use. Symetri then proved that it would be a value-add decision. We could use the collection for analysis, and for CGI, in addition to the AutoCAD functionality we needed.
This was one of those step-change moves for Stanta. We could now show the building with the stud walls in place, which makes projects come alive for clients. We could more clearly communicate to clients the components of our solutions and the benefits they delivered, such as provided by fire barriers, rails, and membranes. On top of these new capabilities came the benefit that we obtained far more functionality for not a lot more financial investment by moving to the AEC Collection”.
Training in how to make the software your own
Although Symetri offers a wide range of scheduled training packages, Stanta has also sought guidance on using various software solutions for very specific workflows it has needed to address within Revit, such as copying sheets, and linking models and drawings to help coordinate gridlines and column locations.
Such customisation training requirements did not need to be formalised in long-duration sessions but were often handled as and when they occurred; an hour here, a couple of hours there—responding to Stanta’s needs as they became apparent through everyday use.
“Symetri are always responsive to our requests even when they’re just for ‘quick-fix’ guidance such as how to locate seemingly missing files and information or schedule materials lists from within Revit”, says Seán.
“What Symetri does, in guiding our designers in some of the more specialised functionalities of software, is enable us to make the software our own; like it was designed just for us. With Symetri’s help, that’s exactly what we’re able to make it become”.
Focusing on what’s right for the business
But even with this reassuring level of support, Seán gained another insight into why Symetri was worthy of the description ‘trusted advisor’: “We’d been issued a PAS[1] project and had identified a certain software solution we felt could help us meet its requirements. We believed it might, but wanted that confirmed by experts, so we asked Symetri.
Then two amazing things happened. Firstly, they supplied the software on a month’s free trial basis and helped us understand how to use it. Secondly, after we had jointly made observations on what it could do for us, Symetri advised us that it was not right for Stanta, it would involve too much designer effort for not enough progress.
The point about this exercise was that Symetri was not sales-driven; it genuinely wanted what was best for Stanta”.
The next phase: Ready for BIM
Transformation: Strong history | Stronger future
Stanta had previously been accustomed to receiving models from architects against which Stanta’s engineers would then create the steel frameworks’ specifications. With much of its project work being in schools and hospitals, Stanta then began to receive BIM models more frequently, given the mandatory requirements to use BIM in public sector projects.
The time had come for Stanta to gain BIM certification, even though it had been working to BIM principles since 2015 with its move into more government-funded projects. Proud of the exceptional nature of its output, and the processes it adhered to in creating it, Stanta now needed to be able to prove it not just through track record but through having the validated credentials to independently verify its capabilities.
Stanta is now under starter’s orders for BIM. The essential first stage is to undertake a BIM Gap Analysis. As Seán says, Symetri’s team has an in-depth knowledge of Stanta’s business, its activities, its workflows, and the needs of the clients it serves. These insights all go to make the BIM Gap Analysis a relatively smooth process but still one that takes about three months.
The detail required by the leading external accreditation and certification bodies is exhaustive, and that means that the preparation has to be equally so.
The Gap Analysis is not just about finding what and where the gaps are either;
it’s also about rectifying the procedures, or documentation,
or digital working practices that facilitate them.
“Our Symetri Account Manager has explained what we can expect during this exercise and I feel there will be the need for change in some of our practices to make sure we conform to the requirements, but this is another area where the value of our long-term connection with Symetri pays dividends.
They have always been the champions of best practice within our business and that puts us in a pretty robust place to start from. We’ve got a strong shared history and that sets the foundations for a stronger shared future”, says Seán.